FlexEChem: Flexible Electrochemical Plant of the Future
Abstract: What kind of reactor design, control and operation technology is needed for a flexible electrochemical plant that runs with high intensity currents and is economically viable?
The above question can only be answered by systematically studying the interactions between process design, control and operations under new circumstances, and integrating the requirements on each of them together with the economic objectives at the early stages of synthesising the electrochemical plant of the future. Therefore, all relevant mechanisms taking place within a representative electrochemical reactor (here referred to as a ‘electrolyzer’) and the process control of this cell should be understood, more specifically;
- How will electrolyzer components be impacted by on/off operation or on/stand‐by variations or continuously varying production? (WP1)
- What are the underlying kinetic and transport phenomena (time and length scales) occurring in the electrolyzer? (WP2)
- How does the intermittency influence process design, control and operations? (WP3)
This project aims to contribute to the electrification of chemicals industry through development of a new integrated approach (integrated process design, control and operations) and a complete process system (reactor, sensors, actuators etc.) for the direct electrochemical conversion of CO2 to C2H4 under industrial conditions.
The complete coupling approach is used to remove the downstream thermochemical process present in the options (a) and (b), which provides more flexibility and less operational constraints. CO2 conversion is also a perfect example of converting a circular raw material into a usable material while the product, C2H4, is a high value base product used in manufacturing of several chemicals.
The project will deliver tools and guidelines for the industrial scale design and operation of electrochemical plants, strategies that currently do not exist in academic or industry at the moment but are critical for a future where renewable electricity is the primary energy source. Although CO2 conversion to C2H4 will be the test case throughout the project, the strategies and knowledge developed are applicable to H2 production from water electrolysis, N2 reduction to NH3 and all electrons to chemical bonds (e‐Refinery) systems.
Coordinator: Prof.dr.ir. J.R. van Ommen
Partners: The FlexEchem consortium comprises of 2 universities, 3 principal investigators, 1 cooperation partner, and 5 industrial partners
Funding Tool: NWA-ECCM, partly government and partly company funding
Duration: 4 years
TUD Workforce: 3 PhD (2 TUD and 1 Tue)
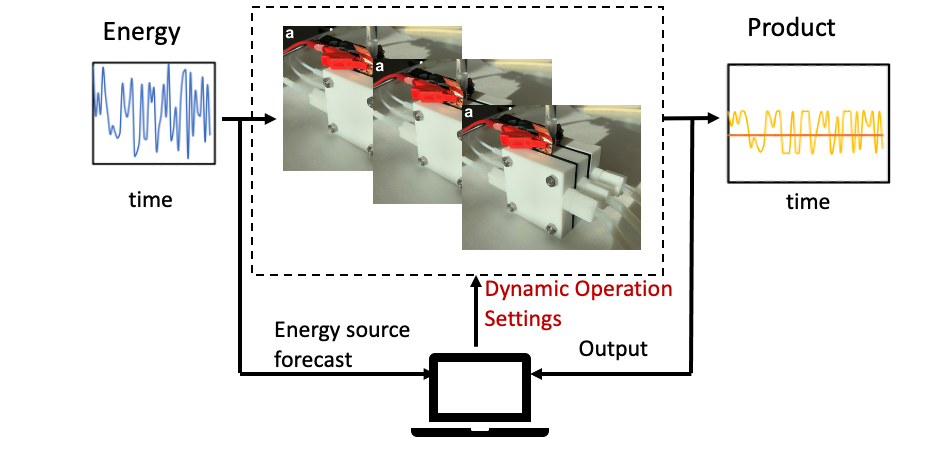