The enormous potential of self-healing bio-concrete
Concrete rot. This is an unflattering (and biologically incorrect) term for an ongoing challenge facing concrete construction. Water penetrates a concrete structure and affects the steel reinforcement within the concrete. Rust causes the steel to expand, bursting the concrete. With its self-healing concrete, TU Delft spin-off Green Basilisk is tackling this problem. The result: fewer repairs and a significant reduction in CO2. Five questions to CEO Bart van der Woerd about this extraordinary innovation.
By Jochen Meischke • September 22, 2023
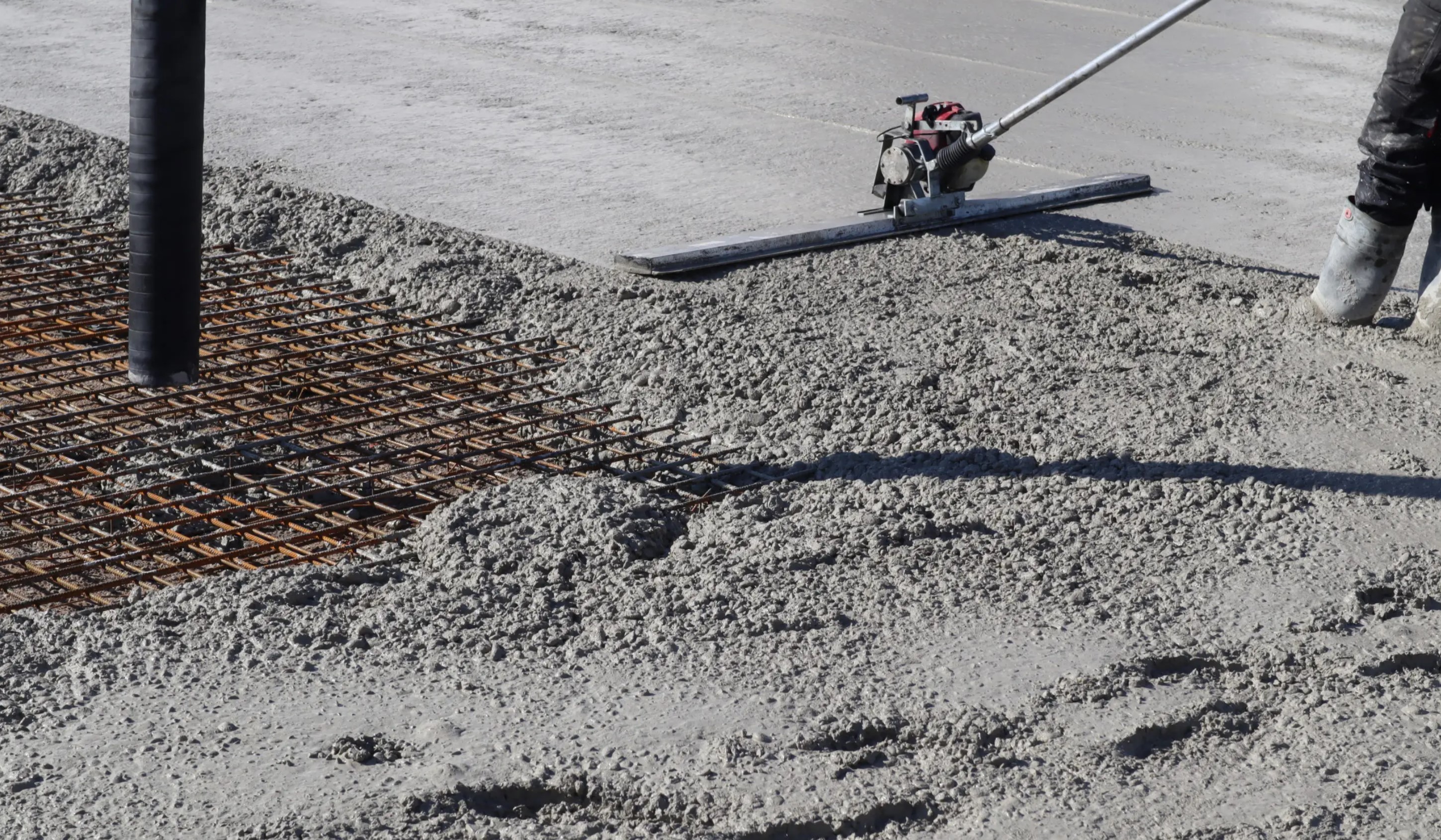
What is self-healing concrete?
Self-healing concrete is also sometimes known as bio-concrete. In this concrete, bacteria spores which release limestone are co-cast into the concrete, explains van der Woerd. “If water penetrates the concrete, this ‘wakes up’ these bacterial spores and they begin to produce limestone. This then fills in the cracks that have appeared in the concrete. This innovation is the brainchild of Henk Jonkers and Erik Schlangen from TU Delft’s Faculty of Civil Engineering and Geosciences.”
Self-healing concrete has the potential to dramatically reduce the cost of repairing existing concrete. “In new builds, it provides better protection against water and less steel reinforcement is needed, saving money and reducing CO2. It’s a game changer for the sector.”
In its search for a suitable candidate to launch this promising innovation onto the market, TU Delft turned to van der Woerd. It is a material that holds few secrets for him: he has decades of experience as a specialist in concrete maintenance and has worked on major infrastructure projects for some of the Netherlands’ largest construction companies.
How does self-healing concrete make it possible to save money?
Worldwide, concrete is one of the most widely used materials. Some eight billion cubic metres of concrete are produced every year: one cubic metre for every world citizen. Much of that concrete has to withstand (salt) water, which makes it susceptible to concrete rot and cracking. Maintenance and repair is a difficult challenge, according to van der Woerd: “A contractor will do the job in accordance with the required specifications and is then out of the picture. If something goes wrong after that, it’s difficult to determine who caused it and who should get the blame. But dangerous cracks in a bridge or building need to be dealt with urgently.”
Prevention is better than cure: when self-healing concrete is used in construction, fewer repairs are needed and construction is possible with 30 to 40% less reinforced concrete: a huge saving in view of the fact that steel is an expensive component in construction and a lot of CO2 is generally released in its production.
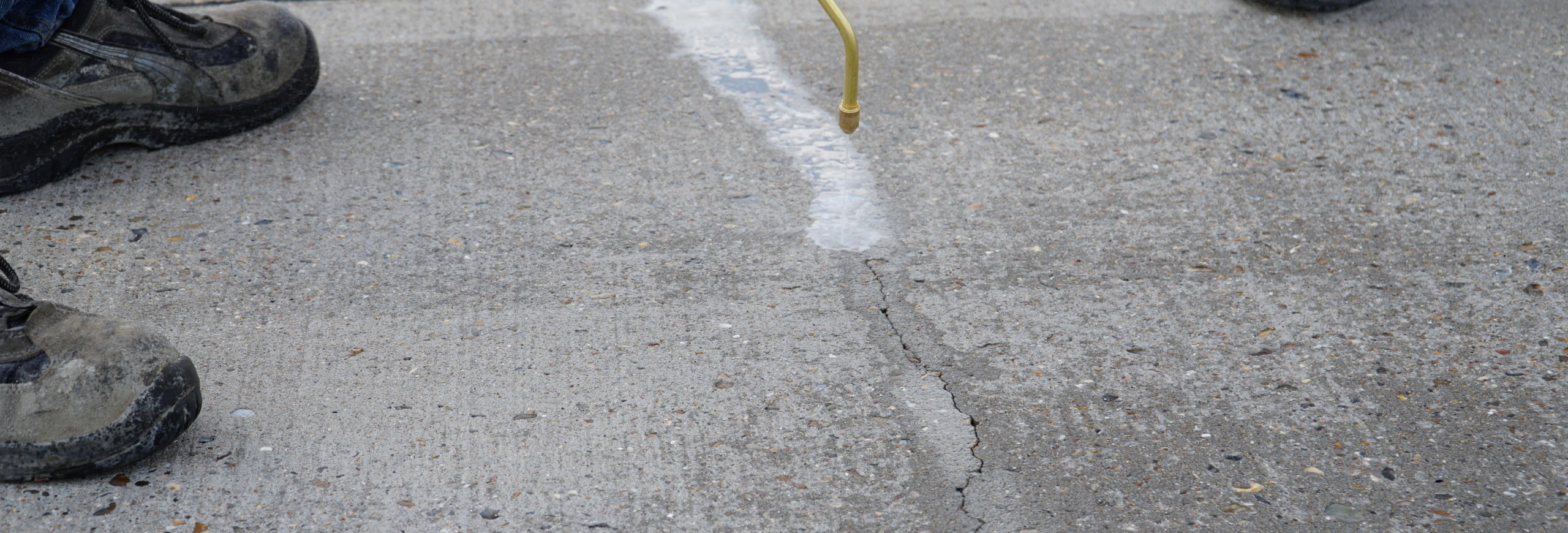
What are the possibilities for use with existing concrete?
The reality is that there is still an awful lot of ‘ordinary’ concrete around in the world. This is why Green Basilisk is not only focusing on self-healing concrete, but also on repair mortar with the same self-healing properties. This makes it possible for existing concrete to be sustainably repaired and made waterproof and reduces the future need for repair – ultimately bringing down the cost of maintenance.
Existing structures require frequent repair but a lot can go wrong, explains van der Woerd. "Especially when using mortar in the repair process. If it doesn’t bond properly, concrete rot can soon reappear. That’s why we’ve made our self-healing mortar fool-proof – with an extremely effective bond." This makes it possible to apply self-healing mortar to existing concrete structures. It is also particularly suitable for waterproofing existing quays and cellars.
What is required in order to accelerate innovation in the concrete industry?
The concrete industry has always been conservative. Companies are accustomed to working in a specific way and are naturally risk-averse. If there are problems in major projects, they can result in expensive damage claims, which is why tried-and-trusted methods are the norm. But change is needed: the sector accounts for over 15% of annual CO2 emissions. Europe also has to meet its Green Deal target: being climate-neutral by 2050. Van der Woerd: “Commissioning authorities are already demanding a smaller footprint and manufacturers, contractors and subcontractors are all gradually beginning to notice that. It will take some effort, but anything worth doing always does.”
At the same time, the Netherlands serves as an excellent living lab, as van der Woerd explains. “In many countries, hierarchical structures can prevent open dialogue. In the Netherlands, we have the confidence to be critical to each other and have high quality standards. Combine that with a close relationship with TU Delft as your partner to accelerate innovations and you have fertile ground for growth. If you can prove yourself in the Netherlands, you’re also ready to take on the rest of the world. And it's outside the country’s borders where you can really make a difference with waterproof, low-maintenance and self-healing concrete.”
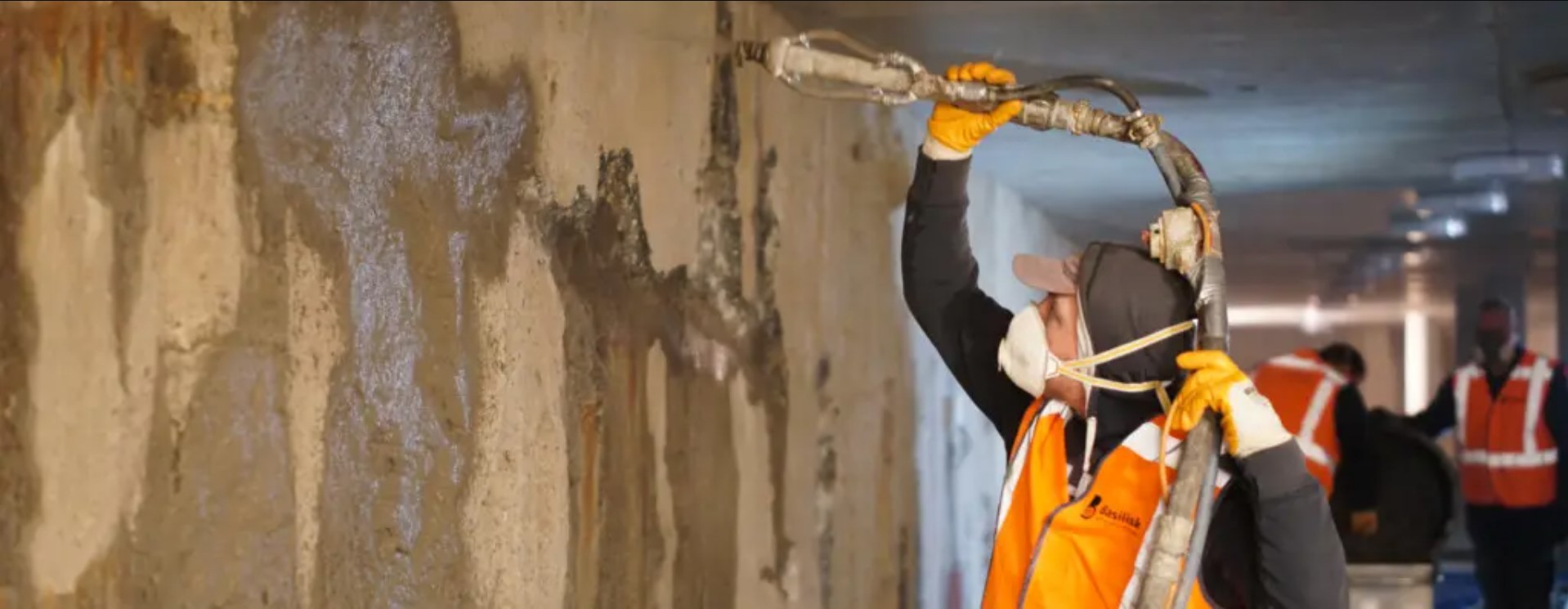
How do you make innovations a successful part of major projects?
The Dutch Concrete Agreement (Betonakkoord) has set a target to reduce CO2 by 50% by 2030. That also presents a major challenge that calls on all the parties involved to dare to take risks. This increases the sense of urgency, says van der Woerd. "We will need innovations to achieve that reduction. But we’re also asking clients and commissioning authorities to take a risk with these innovations. If it goes wrong, it could damage their reputation."
Van der Woerd suggests setting aside a ‘risk fund’ as a feasible alternative for subsidies or carbon pricing within projects: a special fund that you can turn to if something does go wrong with a major project. “The industry, commissioning authorities: everyone's scared of the risks involved in innovation and renewal. And I fully understand that. But a willingness to experiment is essential. In 1911, Anthony Fokker took a huge risk when he flew around the St-Bavo Church several times to prove that his aircraft worked. We still need that kind of daring.”